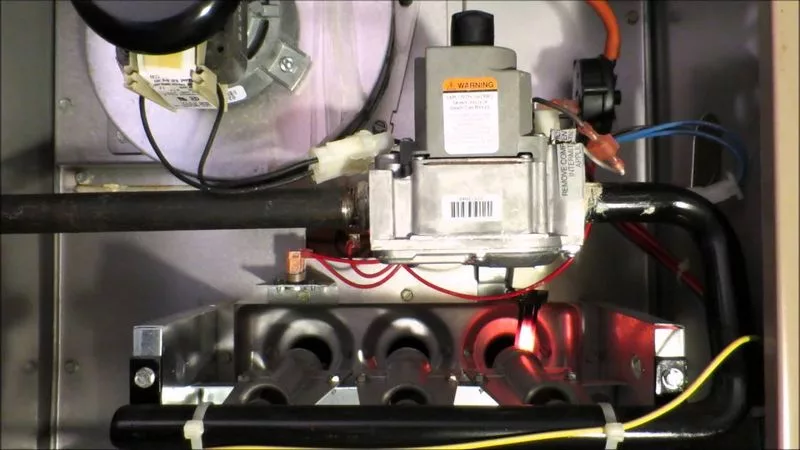
Gas Furnace Sequence of Operation: A Detailed Overview
Understanding the intricate workings of a gas furnace is crucial for anyone involved in its maintenance or repair. One of the key aspects to grasp is the sequence of operation. This detailed overview will provide a complete guide to the various steps that a gas furnace goes through during its operation.
At its core, a gas furnace is designed to provide efficient heating for residential and commercial spaces. To achieve this, it follows a specific sequence of operation that ensures the furnace operates safely and effectively. This sequence involves a series of steps, each playing a vital role in the overall functioning of the furnace.
The sequence starts with the thermostat sensing a drop in temperature and sending a signal to the gas valve to open. This allows the flow of natural gas or propane into the combustion chamber. Once the gas is present, the ignition system, typically a pilot light or an electronic igniter, ignites the gas, creating a controlled flame. This flame then heats up the heat exchanger, which in turn heats up the air.
Once the heat exchanger reaches the desired temperature, the blower motor kicks in, forcing the heated air through the ductwork and into the living or working space. At the same time, the exhaust flue vents the byproducts of combustion, ensuring they are safely expelled outside. Once the thermostat senses that the desired temperature has been reached, it sends a signal to the gas valve to close, stopping the flow of gas and shutting down the furnace.
Understanding this sequence of operation is essential for troubleshooting any issues that may arise. By knowing the various steps involved and the role they play, HVAC technicians can easily identify and rectify any problems, ensuring the efficient and safe operation of the gas furnace.
Understanding the Basics
An overview of the gas furnace sequence of operation is essential for anyone involved in the heating industry. By understanding how a gas furnace operates, technicians can diagnose and troubleshoot potential issues more effectively.
The sequence of operation refers to the specific steps that a gas furnace goes through to produce heat. This process is critical for maintaining a comfortable indoor temperature during colder months. It is essential to comprehend the basics of the gas furnace sequence of operation to ensure optimal performance and energy efficiency.
A gas furnace typically follows the following sequence of operation:
- The thermostat detects that the indoor temperature is lower than the desired set temperature.
- The thermostat sends a signal to the furnace control board.
- The control board initiates the combustion process by turning on the gas valve.
- The gas valve opens, allowing a controlled flow of gas into the burner assembly.
- An electronic igniter or a pilot light ignites the gas, creating a flame.
- The flame ignites the burners, and the combustion process begins.
- The blower motor starts running, pulling air into the furnace.
- The air passes through a heat exchanger, which transfers heat from the combustion process to the air.
- The heated air is then distributed throughout the ductwork and into the rooms of the home via the supply vents.
- The furnace continues to operate until the desired indoor temperature is reached.
- Once the set temperature is achieved, the thermostat sends a signal to the control board to turn off the gas valve and shut down the furnace.
- The blower motor continues to run for a short period to remove any remaining heat from the heat exchanger and distribute it throughout the home.
- Finally, the blower motor shuts off, and the entire gas furnace sequence of operation is complete.
Having a solid understanding of the gas furnace sequence of operation allows technicians to identify and address any issues that may occur throughout the heating process effectively. Regular maintenance and troubleshooting based on this knowledge can ensure the optimal performance and longevity of a gas furnace.
The Role of the Thermostat
In the detailed sequence of operation of a gas furnace, the thermostat plays a critical role. The thermostat is the device responsible for controlling the temperature inside a building by sending signals to the furnace. It acts as the brain of the heating system, constantly monitoring and regulating the temperature according to the desired set point.
When the thermostat detects that the temperature has fallen below the set point, it sends a signal to the furnace to start the heating process. This signal activates the ignition sequence, where the gas valve opens, allowing gas to flow into the burners. The thermostat also initiates the ignition process, sparking the igniter to ignite the gas, creating a controlled flame inside the furnace.
Once the flame is ignited, the thermostat continues to monitor the temperature. As the temperature approaches the set point, the thermostat sends a signal to the gas valve to reduce or stop the gas flow, controlling the amount of heat produced by the burners. This helps maintain a consistent temperature and prevents overheating.
The thermostat also plays a role in the fan operation. Once the desired temperature is reached, the thermostat sends a signal to the blower motor, activating the fan. The fan then circulates the heated air throughout the building, ensuring even distribution of heat. When the thermostat detects that the temperature is above the set point, it signals the blower motor to turn off, stopping the fan operation.
In summary, the thermostat acts as the central control unit in the gas furnace sequence of operation. It monitors the temperature and sends signals to the furnace and blower motor, ensuring a comfortable and controlled indoor environment. Without a properly functioning thermostat, the operation of the gas furnace would be compromised, leading to inefficiencies and potentially uncomfortable conditions.
Heat Exchanger and Ignition
One of the crucial components of a gas furnace and a key element in its sequence of operation is the heat exchanger. The heat exchanger is responsible for transferring heat from the combustion process to the surrounding air that will eventually blow out and heat up the area.
The heat exchanger is a set of metal tubes or pipes, usually made of steel, arranged in a specific pattern to optimize heat transfer. As the fuel burns in the furnace’s combustion chamber, the heat exchanger absorbs the hot gases produced by the combustion process.
The heat exchanger is designed to maximize the contact area between the hot gases and the surrounding air that passes over it. This allows for efficient heat transfer, ensuring that as much heat as possible is extracted from the combustion process and transferred to the air that will be circulated throughout the house.
The ignition process is another integral part of a gas furnace’s sequence of operation. A reliable ignition system is necessary to ignite the fuel and start the combustion process in the furnace. Common types of ignition systems used in gas furnaces include pilot lights and electronic ignition systems.
A pilot light is a small, continuously burning flame that is used to ignite the main burner when a call for heat is initiated. The pilot light is usually located near the burners and is kept lit at all times. When the thermostat signals a need for heat, the gas valve opens, allowing fuel to flow to the burners. The pilot light then ignites the fuel and starts the combustion process.
Electronic ignition systems have become more common in modern gas furnaces. These systems use an electronic control board and various sensors to monitor and control the ignition process. When a call for heat is received, the control board initiates a spark or a hot surface ignition to ignite the fuel and start the combustion process.
Both pilot light and electronic ignition systems are designed to ensure safe and reliable ignition of the fuel in the furnace. They are an essential part of the overall operation of the gas furnace and play a crucial role in delivering warm air to your home.
Air Distribution System
The air distribution system is an essential component of a gas furnace’s operation. It ensures that the heated air produced by the furnace is effectively distributed throughout the space to provide optimal comfort. This system consists of various components that work together to deliver conditioned air to different areas of the building.
One of the key components of the air distribution system is the blower. The blower is responsible for pushing the heated air through the furnace and into the ductwork. It is typically powered by an electric motor and has multiple speeds to accommodate different airflow requirements.
The ductwork is another important element of the air distribution system. It consists of a network of specially designed channels that distribute the heated air to different rooms or zones. The ductwork is typically made of metal or flexible materials and is strategically installed to ensure proper airflow and minimize air leakage.
In addition to the blower and ductwork, the air distribution system also includes various other components such as dampers, filters, and registers. Dampers are adjustable plates or valves that can be used to regulate the flow of air within the ductwork. Filters are used to remove dust, pollen, and other particles from the air before it is distributed. Registers, also known as grilles or diffusers, are the visible parts of the ductwork that allow air to enter or exit the system.
Overall, the air distribution system plays a crucial role in the operation of a gas furnace. It ensures that the heated air is evenly distributed throughout the building, providing consistent comfort to occupants. Proper design, installation, and maintenance of the air distribution system are essential to maximize the efficiency and performance of the furnace.
Gas Furnace Sequence of Operation: Step-by-Step
In this section, we will provide a detailed overview of the operation sequence for a gas furnace. Understanding the step-by-step process can help homeowners and technicians troubleshoot any issues that may arise.
The sequence of operation for a gas furnace can vary slightly depending on the specific make and model. However, the general sequence typically includes the following steps:
Step | Description |
---|---|
1 | The thermostat detects a need for heat and signals the furnace to start. |
2 | The draft inducer motor kicks in, creating a draft to remove combustion byproducts and ensure proper airflow. |
3 | The pressure switch checks for proper venting and allows the ignition sequence to continue if conditions are met. |
4 | The pilot light or ignition system ignites the gas in the burner assembly. |
5 | The flame sensor detects the presence of a flame and sends a signal to the control board. |
6 | The gas valve opens, allowing gas to flow to the burners. |
7 | The main burners ignite, producing heat to warm the air. |
8 | The blower motor starts and circulates the heated air through the ductwork and into the living spaces. |
9 | The limit switch monitors the temperature inside the furnace and shuts off the burners if the temperature exceeds the set limit. |
10 | Once the thermostat reaches the desired temperature, it signals the furnace to shut off. |
Understanding the gas furnace sequence of operation can be helpful when troubleshooting issues such as no heat, frequent cycling, or inadequate airflow. By identifying where in the sequence the problem occurs, homeowners or technicians can pinpoint the cause and make the necessary repairs or adjustments.
It’s important to note that this overview provides a general sequence of operation and may not apply to every gas furnace. Consulting the manufacturer’s documentation or contacting a licensed technician is always recommended for specific troubleshooting or maintenance guidelines.
Thermostat Calls for Heat
The operation of a gas furnace is initiated when the thermostat in the home calls for heat. The thermostat, which is typically located on an interior wall, detects the temperature in the room and sends a signal to the furnace to start the heating process.
When the thermostat detects that the temperature has fallen below the set point, it sends an electrical signal to the furnace’s control board. This signal triggers the start of the furnace sequence of operation.
The control board receives the signal from the thermostat and begins the process of igniting the gas in the furnace. This is done by opening the gas valve and igniting the gas with a spark or pilot light.
Once the gas is ignited, the control board monitors the flame using sensors. If the flame is detected, the control board continues the sequence of operation. If the flame is not detected, the control board will shut off the gas valve to prevent a dangerous buildup of gas in the furnace.
During the heating process, the control board also operates the blower fan to circulate the heated air throughout the home. The blower fan helps to distribute the warm air evenly and efficiently.
The thermostat continuously monitors the temperature in the room and communicates with the control board to maintain the desired set point. Once the temperature reaches the set point, the thermostat will stop calling for heat and the gas furnace will enter a standby mode until it is called for heat again.
In conclusion, the detailed sequence of operation for a gas furnace starts when the thermostat calls for heat. The furnace control board responds to the thermostat’s signal by igniting the gas and operating the blower fan to distribute the heated air. The thermostat continuously monitors the temperature and communicates with the control board to maintain the desired set point.
Inducer Motor Starts
Once the gas furnace receives a call for heat, the first step in the sequence of operation is for the inducer motor to start. The inducer motor is responsible for drawing air into the furnace and creating the necessary draft for combustion.
When the thermostat detects a need for heat and sends a signal to the furnace control board, the inducer motor is energized. This motor is typically a small, single-speed motor that is directly connected to the blower wheel and combustion chamber. It is designed to run at a specific speed to create the proper airflow.
As the inducer motor starts, it spins the blower wheel, which pulls air into the combustion chamber. The air intake may be located on the side or bottom of the furnace cabinet. The inducer motor also creates a negative pressure within the furnace, which helps to vent any combustion gases from the previous heating cycle.
The inducer motor is often equipped with a pressure switch. This switch ensures that the inducer motor is running and creating the necessary draft before allowing the rest of the sequence of operation to continue. If the pressure switch does not detect the proper amount of negative pressure, it will prevent the furnace from igniting for safety reasons.
Overall, the inducer motor starting is a crucial step in the gas furnace sequence of operation. It initiates the proper airflow and creates the necessary draft for combustion to occur safely and efficiently.
Pressure Switch Verification
In a gas furnace, the pressure switch is an important component that ensures the safe operation of the furnace. The pressure switch verifies that the combustion chamber has the appropriate amount of air flow before allowing the furnace to ignite.
During the sequence of operation, the pressure switch is constantly monitored to ensure that it is functioning properly. If there is a problem with the pressure switch, the furnace will not ignite to prevent any potential safety hazards.
Verification of the pressure switch involves several steps:
1. Visual Inspection: The pressure switch should be visually inspected for any signs of damage or corrosion. Any visible issues should be addressed and repaired before proceeding.
2. Electrical Testing: Using a multimeter, the continuity of the pressure switch contacts should be tested to ensure that they are functioning correctly. If there is no continuity, it indicates a faulty pressure switch that needs to be replaced.
3. Pressure Testing: A manometer is used to measure the pressure at the inlet and outlet ports of the pressure switch. The pressure readings should match the specified range for the particular furnace model. If the pressure is outside of the range, it indicates a problem that needs to be addressed.
4. Wiring Inspection: The wiring connections to the pressure switch should be checked to ensure that they are secure and properly connected. Loose or damaged wiring can lead to faulty operation.
5. Functional Testing: The furnace should be tested to verify that the pressure switch is opening and closing as it should during the sequence of operation. This can be done by simulating different scenarios and monitoring the behavior of the pressure switch.
By verifying the pressure switch, the furnace’s sequence of operation can be assured to proceed safely and efficiently. Regular maintenance and inspection of the pressure switch can help prevent any potential issues and ensure the continued reliable operation of the gas furnace.
Hot Surface Ignition or Pilot Flame Ignition
In the detailed overview of the gas furnace sequence of operation, two common methods of igniting the gas are hot surface ignition and pilot flame ignition.
Hot surface ignition is a more modern and efficient method of igniting the gas in a furnace. It uses a hot surface igniter that is powered by electricity. When the thermostat signals for heat, the control board sends a signal to the hot surface igniter, which then heats up. The hot surface igniter becomes red hot and ignites the gas as it passes over it. This method does not require a pilot flame and is more reliable and efficient.
In contrast, pilot flame ignition is an older method that uses a small gas flame, known as a pilot light, to ignite the main burner. When the thermostat signals for heat, a small amount of gas is released and ignited by the pilot flame. Once the pilot flame is established, it then ignites the main burner. This method requires a constant flame to keep the pilot light burning and can be less efficient than hot surface ignition.
Overall, hot surface ignition is preferred in modern gas furnaces due to its reliability and efficiency. It eliminates the need for a pilot flame and provides a more consistent ignition source. Pilot flame ignition, on the other hand, is still used in older furnaces but is less common in newer models due to its lower efficiency.
Main Burner Ignition
Once the gas furnace has completed its startup sequence, the main burner ignition process begins. This is a crucial part of the overall operation of the furnace, as it is responsible for generating the heat necessary to warm the air that will be circulated throughout the building.
Once the sequence has reached the point of main burner ignition, the gas valve opens, allowing fuel to flow into the combustion chamber. At the same time, the igniter, typically a hot surface igniter or a spark igniter, begins to heat up. The purpose of the igniter is to provide a source of ignition for the gas as it enters the combustion chamber.
As the igniter heats up, it reaches a temperature where it is able to ignite the gas. Once the gas is ignited, the main burner flames are established and begin to heat up the heat exchanger. The heat exchanger is a vital component of the furnace, as it is responsible for transferring the heat from the combustion process to the air that will be distributed throughout the building.
During the main burner ignition process, it is important to ensure that the ignition is successful and that the flame is stable. A flame sensor is typically used to monitor the presence of the main burner flame. If the flame goes out for any reason, the flame sensor will quickly detect this and send a signal to the control board, which will shut off the gas supply to the main burner and initiate a safety shutdown procedure.
It is also important to note that the main burner ignition process is typically controlled by a sequence of safety devices and control components. These devices and components work together to ensure that the main burner ignition occurs safely and efficiently. They monitor various parameters, such as gas pressure, ignition temperature, and flame presence, to ensure that the furnace is operating within safe limits.
The main burner ignition is a crucial step in the gas furnace operation sequence. It is responsible for igniting the gas and establishing the main burner flames, which generate the heat needed to warm the air. Proper ignition is essential for the furnace to operate safely and efficiently.
Heat Exchanger Heats Up
The heat exchanger plays a crucial role in the operation of a gas furnace. It is responsible for transferring heat from the combustion gases to the air that is circulated throughout your home. Understanding how the heat exchanger works is essential for a detailed overview of the furnace’s sequence of operation.
The heat exchanger is made up of a series of metal tubes or coils that are arranged in a way that maximizes the contact between the hot combustion gases and the air. When the furnace is turned on, the burners ignite and produce flames that heat up the exchanger. As the hot combustion gases pass through the exchanger, the metal tubes or coils heat up.
The heated exchanger then comes into contact with the cool air from your home’s return air ducts. As the air moves over the heated exchanger, the heat is transferred from the metal to the air. This process is known as convection, and it is what allows the furnace to heat your home.
It’s important to note that the heat exchanger must be in good condition for the furnace to operate safely and efficiently. If there are any cracks or leaks in the exchanger, it can lead to the release of carbon monoxide into your home’s air. Carbon monoxide is a colorless and odorless gas that can be extremely dangerous, so it’s crucial to have regular inspections and maintenance performed on your furnace.
The heat exchanger is a vital component of a gas furnace’s operation. It allows for the transfer of heat from the combustion gases to the air that is circulated throughout your home. Understanding how the heat exchanger heats up is essential for a detailed overview of the furnace’s sequence of operation.
Blower Motor Starts
Once the gas furnace ignites and the burners produce heat, the next step in the sequence of operation is the start of the blower motor. The blower motor is responsible for circulating the heated air throughout the home or building.
When the blower motor starts, it creates a steady flow of air over the heat exchanger, which allows for efficient transfer of heat from the combustion process. This ensures that the air that is distributed into the living spaces is warm and comfortable.
The blower motor is typically activated by the furnace control board in response to a signal from the thermostat. The control board sends a low voltage signal to the blower motor relay, which then energizes the blower motor. Once the blower motor is energized, it begins to spin at a set speed determined by the blower motor settings.
In some furnaces, the blower motor speed can be adjusted to meet the specific heating needs of the home. This can be done manually or automatically, depending on the type of furnace and its controls. The blower motor speed can also be adjusted to accommodate the different stages of operation, such as low speed for heating and high speed for cooling.
During the operation of the blower motor, it is important to ensure that the air filters are clean and free from debris. Dirty air filters can restrict the airflow, causing the blower motor to work harder and potentially overheat. Regular maintenance and cleaning of the filters is essential to keep the blower motor running smoothly and efficiently.
The blower motor start is a crucial step in the sequence of operation of a gas furnace. It plays a vital role in circulating the heated air throughout the home or building, ensuring comfort and efficiency. Regular maintenance and cleaning of the blower motor and air filters are essential to keep the system running smoothly.
Limit Switch Verification
In the gas furnace sequence of operation, the limit switch plays a crucial role in ensuring the safe and efficient operation of the furnace. It is responsible for monitoring the temperature inside the furnace and preventing the system from overheating.
During the furnace operation, the limit switch constantly monitors the temperature. If the temperature exceeds the predetermined limit, the limit switch will interrupt the sequence and shut off the burner to prevent any potential damage or hazards.
To verify the proper functioning of the limit switch, follow these steps:
- Turn off the gas supply: Before performing any maintenance or inspection, make sure to turn off the gas supply to the furnace to ensure safety.
- Access the limit switch: Locate the limit switch, which is usually positioned near the heat exchanger or blower compartment of the furnace.
- Inspect for any visible damage or debris: Check the limit switch for any signs of damage, such as cracks or corrosion. Also, ensure that there is no debris obstructing the switch.
- Test the limit switch: With the power to the furnace turned on, use a multimeter to test the continuity of the limit switch. Place the multimeter’s probes on the terminals of the switch and check for continuity. If there is continuity, the switch is functioning properly. If not, it may need to be replaced.
It is essential to perform regular maintenance and inspection of the limit switch to ensure its proper operation. If you notice any issues or suspect a malfunction, it is recommended to contact a professional HVAC technician for further diagnosis and repair.
Note: Always refer to the manufacturer’s instructions and guidelines when performing any maintenance or repairs on the gas furnace.
Air Distribution
The air distribution sequence in a gas furnace operation is a crucial aspect of its detailed functioning. Once the furnace starts its operation, the primary goal is to distribute warmed air systematically throughout the designated space. This process ensures a comfortable and consistent temperature throughout the building.
After the gas furnace ignites and heats the air, a blower fan is activated to push the heated air through the ductwork system. The fan’s rotation creates suction, which draws in colder air from the return ducts. This return air then passes through the furnace’s heat exchanger, where it is warmed before being distributed.
The warmed air is forced into the supply ducts, which then deliver it to various rooms or zones within the building. The distribution of air can be regulated by dampers within the ductwork, controlling the flow of air to different areas. These dampers are either manually adjusted or controlled automatically based on thermostat settings.
Proper air distribution is crucial for ensuring that the conditioned air reaches all areas evenly, preventing hot or cold spots within the building. It also helps maintain a healthy indoor environment by ensuring proper ventilation and air exchange.
In summary, the air distribution process in a gas furnace sequence of operation is a detailed and essential part of its functioning. By achieving a balanced airflow and adequate distribution, it creates a comfortable and consistent indoor environment throughout the building.
Q&A:
How does a gas furnace work?
A gas furnace works by burning natural gas to produce heat. The gas is ignited by a pilot light or an electronic ignition system, and the heat is transferred to the air by a heat exchanger. The blower fan then distributes the warm air throughout the home via the ducts.
What happens if the draft inducer motor fails?
If the draft inducer motor fails, the gas furnace will not be able to start. The draft inducer motor is responsible for creating a draft in the flue pipe to ensure proper exhaust ventilation. Without the draft inducer motor, the furnace may not ignite or may produce unsafe levels of carbon monoxide.
Why is the flame sensor important in a gas furnace?
The flame sensor is an important safety component in a gas furnace. It is responsible for detecting the presence of the flame. If the flame sensor does not detect a flame, it will shut off the gas valve to prevent the furnace from continuing to burn gas without a flame. This helps to prevent a buildup of unburned gas and potential safety hazards.
What role does the limit switch play in a gas furnace?
The limit switch is a safety device in a gas furnace that monitors the temperature of the heat exchanger. If the temperature exceeds a safe limit, the limit switch will shut off the gas valve to prevent overheating and potential damage to the furnace. The limit switch also controls the operation of the blower fan, starting it when the heat exchanger reaches a sufficient temperature.